Precise camera module manufacturing and testing
Overcoming critical challenges
Sign up here to watch the full video.
Date: November 8, 2018
Duration: 60 minutes
Short preview
About this event
The demand for high quality camera modules is growing steadily. The increased application of camera systems for safety-related and automated object recognition and classification, for instance in the safety & surveillance business and in the automotive industry (keyword: autonomous driving and driver assistance systems), results in new and sometimes greater requirements for the characterization of camera modules. However, the serial production of high-precision optical sensor systems poses a series of critical challenges. Tight mechanical machining tolerances are required to achieve the requested imaging quality. Only a controlled automated manufacturing process which combines all required production steps in one system assures accurate, repeatable and fast camera module alignment and assembly.
Automated active alignment approaches help to optimize production efficiency i.e. higher product quality and higher yield at lower production costs. With ProCam® Align Smart TRIOPTICS offers a complete solution to actively align, assemble and test complex camera modules in order to control and overcome critical issues.
At the beginning of the online event the ProCam® Align Smart production process including glue dispensing, active alignment, and UV-curing is outlined and the specifications, especially regarding the alignment process and its accuracy, are looked at in detail. Also, the possibilities to align lens to sensor board as well as sensor board to lens are explained.
Another focus is then on the relevance of a functional lens and sensor board design. Aspects such as the width of the bearing surfaces, the surface texture itself and the width of the adhesive gap are of great importance for the efficiency and the quality of the alignment process and need to be addressed early in the course of a camera module alignment project.
In the end of the online event the challenge of adhesive shrinkage is outlined. This aspect has a decisive influence on the final image quality of the assembled and cured camera module. By remeasuring the camera module after final curing, the adhesive shrinkage is identified and then taken into account in the upstream gluing process.
The information of this online event is presented in a dialogue between the moderator and the expert using animated charts for demonstrating technical details, video sequences and live demos directly at the ProCam® Align Smart instrument. After the live presentation of the solutions, participants are given the chance to have individual questions answered in a Q&A session.
Expert:
Dipl. Ing. (FH) Benjamin Stauss
R&D Engineer Automation Group
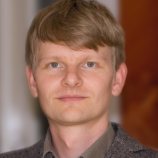
Benjamin Stauss has obtained a diploma degree in Optics & Image Processing at the University of Applied Science in Darmstadt, Germany. Before he started at TRIOPTICS he has developed optical concepts for car headlamps.
At TRIOPTICS he is developing methods for the characterization of camera sensors and modules in active alignment and end of line testing systems for the ProCam® and CamTest group.
Moderator:
Soenke Tanz
Sales Engineer ProCam®
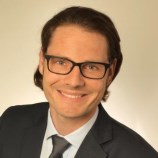
Soenke Tanz has obtained a diploma degree in industrial engineering from the NORDAKADEMIE Universitiy of Applied Sciences in Germany. Soenke has long experience in sales with special focus on the Asian market.
In April 2018, he joint TRIOPTICS to support the sales team in Wedel. His core products are ProCam® and ImageMaster® PRO.